Ensuring Accuracy and Competence in ISO 9001 QMS: A Guide to Measuring Equipment and Training
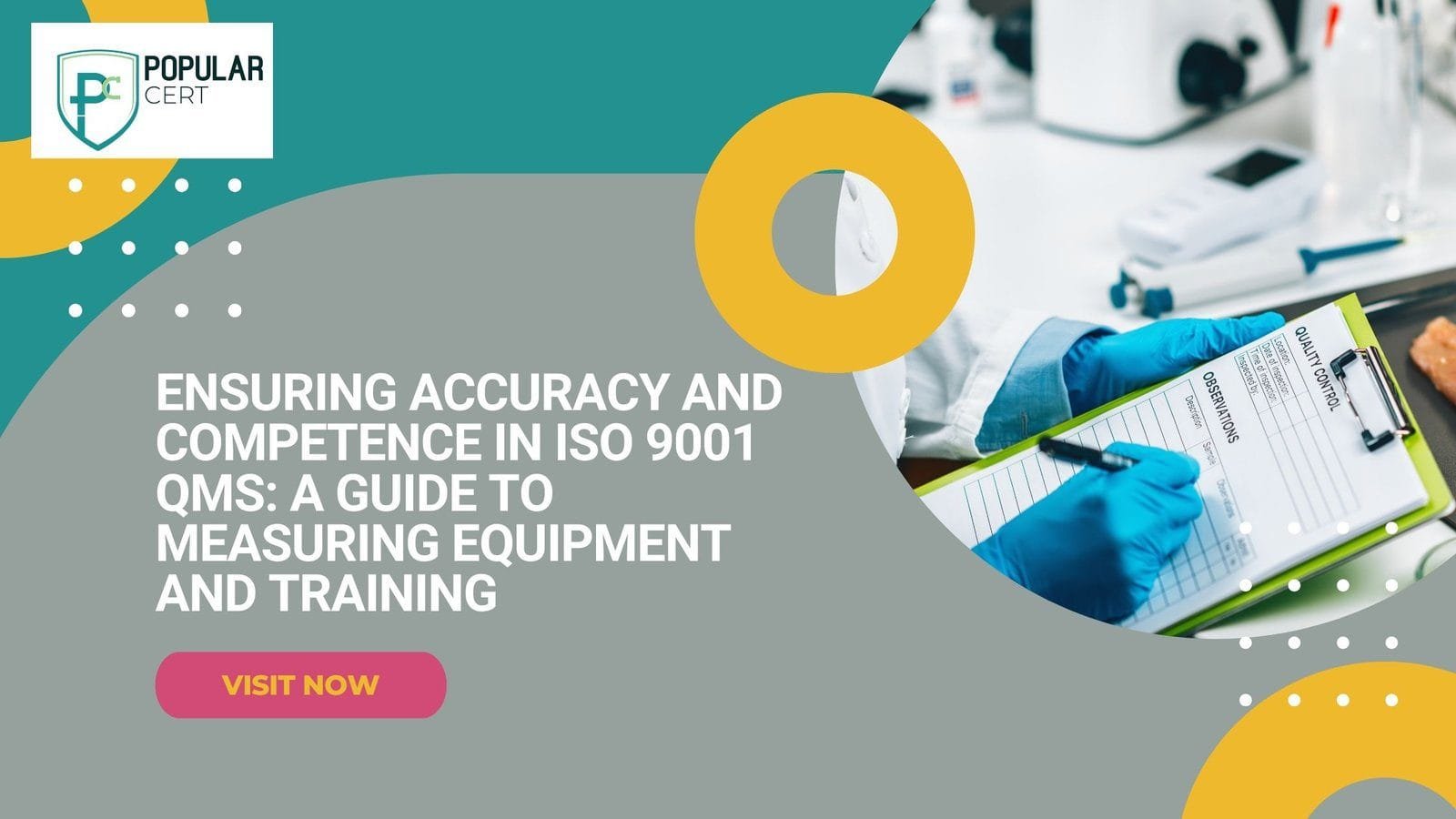
Introduction
In a Quality Management System (QMS), accuracy and competence are critical for delivering consistent, high-quality products and services. From ensuring measuring equipment is properly calibrated to training employees to meet organizational needs, these elements form the backbone of an effective QMS. This blog explores how organizations can maintain accurate measurements, manage calibration, and build a skilled workforce to meet current and future challenges. Whether you’re a small business or a large enterprise, these practices will help you stay compliant, competitive, and customer-focused.
Measurement equipment:
The organization should consider how skilled the personnel who use the measuring equipment need to be and any training they might need.
For example, the manufacturing of parts for cars has a requirement to measure to an accuracy of one tenth of a millimeter (0.1 mm), a dressmaker may require an accuracy of one millimeter (1 mm) and a road builder may have a tolerance of 50 mm on the width of a road.
Another example is the use of a GO/NO-GO gauge when a precise quantifiable measurement cannot be obtained or is not really necessary and an indication of acceptability (i.e. GO) or non-acceptability (NO-GO) is all that is required.
- To make sure the measuring equipment operates effectively and gives reliable results, the organization need
- to make sure it is properly maintained, regularly calibrated and adjusted as needed,
- to describe how this will be done so that records are available which show calibration is traceable to international standards, and
- to make sure it is possible to identify which measuring equipment has been calibrated and that it is suitable for use (e.g. label the measuring equipment).
If measuring equipment is found to be faulty, the organization has to find out at what stage it went wrong. The organization also needs to decide whether you should do anything about the product you have passed using that measuring equipment.
The results of any review could indicate that no action is required or that a product recall is required.
Small organizations are usually faced with the choice of carrying out the calibration themselves or having someone else do it for them.
If the organization decides to carry out its own calibrations, they will need to have procedures for calibrating each type of measuring equipment they use.
If the organization decide to use a supplier, in addition to the points raised they will also need to consider some of the following points
- Ideally, the organization should be endorsed as a calibrating service by a suitable accreditation body.
- The organization should issue a certificate of calibration, which states the uncertainty of measurement (This is another way of stating how accurately the instrument can measure)
- The certificate should indicate that the organization can trace its calibration back to a national or international standard.
It may be possible, if the organization has several pieces of similar measuring equipment, for the most accurate of these to be calibrated by a supplier and then used as the basis for calibration of the others. For example, an accurately calibrated digital thermometer can be suitable as a reference standard for other less accurate temperature measuring equipment.
Calibration:
Calibration is an expensive operation. For a small organization, the costs of calibration can be considerable. The organization should ensure, therefore, that they know the difference between checking that process control measuring equipment is fit for purpose and calibrating measuring equipment which is required to give confidence in its inspection and measurement results.
In some organizations, it is common practice for employees to use their own personal measuring equipment (e.g. steel tapes. micrometers and Vernier callipers). When this occurs, it does not absolve the organization from ensuring that such measuring equipment is calibrated when it is used for release of product.
The solutions are to either ban the use of employee measuring equipment or to calibrate it. The employee should be asked for consent for calibration of the measuring equipment.
 In addition to calibrating and measuring equipment, records need to be kept to show-
- when the measuring equipment was last calibrated, who did it, the calibration procedure, the acceptance criteria, what the result was, its acceptability and how this affects the measuring equipment suitability (calibration status), and
- when the next calibration is due; this period depends on the type of measuring equipment, its usage and how critical the measurements are for control of a process or for verification of product conformity to requirements.
Measuring equipment should be suitably stored when not in use, to protect it from damage or deterioration. It should also be suitable for use in the proposed operating environment.
These precautions apply, in particular, to any master measuring equipment or reference standards used for calibration purposes. Test software may be used to assess product conformance.
Software does not experience drift or aging; however, it can be subject to degradation, viruses or unintended programming errors.
Often, it is impossible for an organization, particularly a small organization to conduct a full validation of a piece of software, therefore, they should take appropriate care when specifying and selecting software (i.e. use a reliable supplier).
Test software might need some form of validation to make sure that it can perform the required measurements, and re-validation to ensure its continuing ability to perform the required measurements. One way is to ensure that this software can accurately and reliably identify products with a known set of faults and deficiencies. Alternatively, from time to time the organization should carry out test runs with known data sets and known results, to see if the test produces matching outputs.
The organization should record the methods you use to validate the software.
Some type of secure write protection should be used on test software, in the same manner as seals are used on hardware calibration adjustments, to minimize inadvertent adjustments.
According to Clause 7.1.6 - Organizational Knowledge
Top management should assess how the organization’s current knowledge base is identified and protected. Top management should also consider how to obtain the knowledge required to meet the present and future needs of the organization from internal and external sources, such as academic and professional institutions.
There are many issues to consider when defining how to identify, maintain and protect knowledge, such as
learning from failures, near miss situations and successes,
capturing the knowledge and experience of people in the organization,
gathering knowledge from customers, suppliers and partners.
capturing undocumented knowledge (tacit and explicit) that exists within the organization,
ensuring the effective communication of important information content (particularly at each interface in the supply and production chains), and managing data and records.
According to Clause 7.2 - Checking Competence and Training
The organization should regularly assess the experience, qualifications, capabilities and abilities of individuals relative to the skills and qualifications needed by the organization for current and foreseeable activities.
By comparing the current competence of personnel against what is required, the organization is performing a competence gap analysis. The gaps need to be filled through training, or by acquiring extra competence through permanent staff to recruitment or fixed term employment contracts.
If the organization chooses to train its own people, they probably will need both training and experience before they can be considered competent.
Work allocation and assignment of personnel, management review, corrective action, risk assessment and internal quality or audit are all likely to identify areas which could indicate a lack of training.
Considerations of skills and aptitudes required under operation (clause 8) could also indicate additional training needs.
It could be useful to plan for training, which then may be carried out in stages. This could consist of a training period followed by a period of familiarization, followed by further training and familiarization.
Training in quality techniques, particularly internal auditing is highly desirable if full advantage is to be taken of the potential that quality management can provide to the organization.
Training may be at the actual workplace, in-house or at some external location. Depending on the topics, undertaking relevant personal development or attending a seminar can also provide worthwhile training.
The organization also needs to evaluate the effectiveness of the actions taken because it is not sufficient to give/receive training and keep a record of it (such as an attendance list).
Certain tasks can require a specific level of competence before they can be performed properly or safely (e.g. internal quality auditing, welding, or non-destructive testing). It might be necessary for people to be qualified for some tasks (e.g. forklift or truck driving, or surveying).
Record Maintaining:
The organization needs to maintain records that provide evidence of an employee’s competence. The organization also needs to keep records of the training an employee has received and any results of that training. The records that show the successful completion of a training program and that competence has been demonstrated can be as simple or as complex as necessary.
Where employees have a formal certified education, e.g. vocational training as mechanic or a university degree, such certification can be a record to demonstrate that the employees have a part of or all of competence required regarding any work included in their education.
Conclusion
Accurate measurements and a competent workforce are essential for a successful QMS. By ensuring proper calibration of equipment, maintaining records, and addressing training gaps, organizations can improve quality, reduce risks, and meet customer expectations. Regular assessments, effective training programs, and clear documentation are key to building a resilient and efficient system. Start implementing these practices today to strengthen your QMS and drive long-term success.
Types Of Certification
- ISO Certification
- ISO 9001 Certification
- ISO 14001 Certification
- ISO 45001 Certification
- ISO 22000 Certification
- ISO 27001 Certification
- ISO 17025 Certification
- ISO 13485 Certification
- ISO 20000-1 Certification
- ISO 22301 Certification
- ISO 50001 Certification
- ISO 37001 Certification
- IATF 16949 Certification
- ISO 29001 Certification
- ISO 31000 Certification
- ISO 20121 Certification
- ISO 10002 Certification
- ISO 41001 Certification
Get Free Consultation
Our Clients
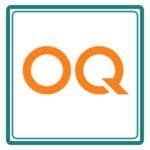
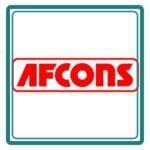
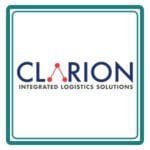
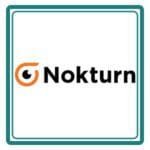

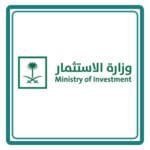
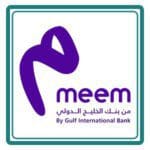
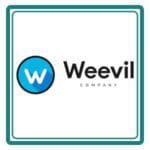
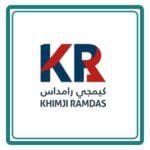
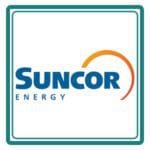
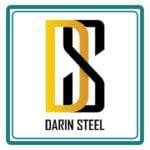
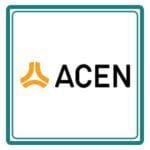
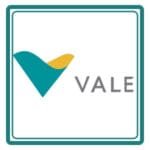
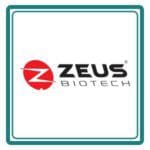
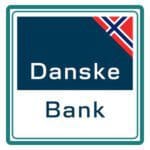

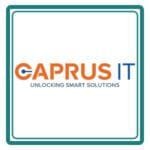
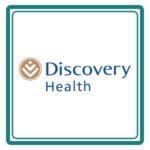
GET A FREE CONSULTATION NOW
FAQ
Why is calibration important in a QMS?
Calibration ensures that measuring equipment provides accurate and reliable results, which is critical for maintaining product quality and meeting compliance standards like ISO 9001.
Can small organizations handle calibration internally?
Yes, but it requires proper procedures, trained personnel, and traceable records. Many small organizations prefer outsourcing calibration to accredited service providers to save costs and ensure accuracy.
What should be included in calibration records?
Records should include the date of calibration, who performed it, the procedure used, acceptance criteria, results, and the next calibration due date.
How can organizations address employee competence gaps?
By conducting regular competence gap analyses, providing targeted training, and maintaining records of employee qualifications and training outcomes.
What is the role of software in measurement and testing?
Test software can help assess product conformance, but it must be validated to ensure accuracy. Organizations should also protect software from unauthorized changes or errors.