ISO 13485 Certification in lebanon
Get Free Consultation
PopularCert delivers expert ISO 13485 certification services in Lebanon, helping medical device manufacturers align with international regulatory expectations. ISO 13485 certification in Lebanon ensures compliance with the ISO 13485 standard, which governs Quality Management Systems specific to the medical device industry. Businesses in key cities such as Beirut, Tripoli, and Sidon benefit from our tailored support in documentation, risk control, and audit readiness. This certification enhances product reliability, ensures regulatory alignment, and builds trust in both local and international healthcare markets.
What is ISO 13485 Certification?
ISO 13485 certification is an international standard for quality management systems in the medical device industry. It ensures that organizations consistently design, develop, produce, and deliver safe and effective medical devices. This certification boosts compliance with global regulations, enhances product quality, and builds trust with patients, healthcare providers, and regulatory bodies across international markets.
Why Is ISO 13485 Certification Important in Lebanon?
- In Lebanon’s growing healthcare and medical device sector, ISO 13485 certification plays a vital role in building trust. It shows that a company consistently meets international quality and safety standards in producing medical equipment. This is especially important for hospitals, labs, and manufacturers who want to assure patients and regulators of product reliability.
- Beyond reputation, ISO 13485 helps Lebanese businesses improve internal operations. It promotes risk management, cleaner documentation, and better control of processes. In a country aiming to boost its medical exports and compete globally, this certification acts as a powerful signal of professionalism. Whether serving local hospitals or international clients, ISO 13485 adds confidence and opens new growth opportunities for Lebanon’s medical industry.
How to Get ISO 13485 Certification In Lebanon?
Process to Get ISO 13485 Certification In Lebanon
Consultation and Gap Analysis
Start by evaluating your existing processes, policies, and quality management practices against the ISO 13485 standard. Identify gaps in compliance, such as missing documentation, inadequate risk management processes, or untrained staff, to create a focused implementation plan.
Implementation
Develop and implement the necessary processes to meet ISO 13485 requirements. This includes establishing robust quality procedures, ensuring proper documentation, incorporating risk management, and training employees on QMS policies. Proper implementation ensures seamless integration of quality management into daily operations.
Internal Audit
Conduct internal audits to assess the effectiveness of the implemented QMS. This step identifies non-conformities or weaknesses, which can then be addressed before the final certification audit. Internal audits are crucial for ensuring compliance and operational readiness.
Management Review
The organization’s top management reviews the QMS to ensure its alignment with business objectives and ISO 13485 requirements. This step ensures that the system is functioning effectively and ready for certification.
External Certification Audit and Certification
Engage an accredited certification body to perform a thorough external audit. Once the system meets all ISO 13485 requirements, certification is granted.
Benefits of ISO 13485 Certification in Lebanon
- Regulatory Compliance: ISO 13485 certification ensures adherence to international regulatory requirements, simplifying market entry and avoiding penalties or legal issues.
- Enhanced Product Quality: The certification helps establish robust processes for manufacturing medical devices, resulting in consistent quality and improved reliability.
- Market Access: ISO 13485 certification is often a prerequisite for exporting medical devices to international markets, opening doors to global opportunities.
- Customer Trust: Certification demonstrates a commitment to quality and patient safety, building trust among customers, stakeholders, and healthcare providers.
- Risk Reduction: The standard emphasizes risk management in design, manufacturing, and distribution, reducing the likelihood of defects or recalls.
- Operational Efficiency: Streamlined processes, better resource management, and reduced errors lead to improved efficiency and cost savings.
- Competitive Advantage: ISO 13485 certification sets your organization apart from competitors, providing a distinct edge in the marketplace.
- Continuous Improvement: The certification encourages ongoing evaluation and enhancement of quality management processes, ensuring sustained excellence.
Types Of ISO Certifications In Lebanon
Get Free Consultation
Our Clients
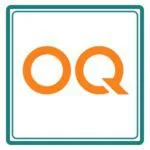
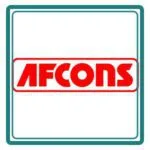
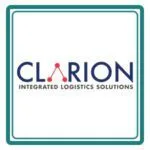
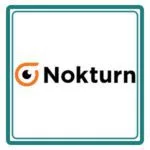
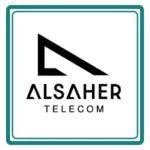
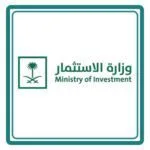
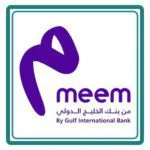
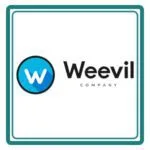
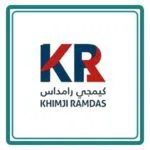
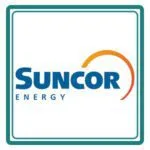
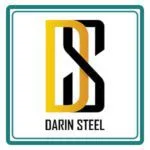
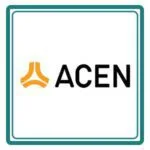
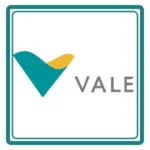
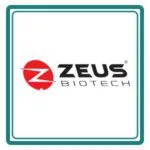
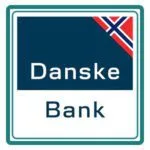

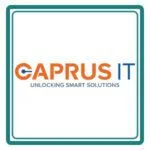
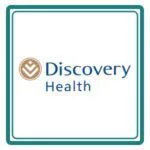
Cost of ISO 13485 Certification in Lebanon
The cost of ISO 13485 certification in Lebanon depends on various elements like your organization’s size, medical product range, and current quality system. Companies aiming for compliance and market access often consult with top ISO 13485 consultants in Lebanon for clarity and cost-efficiency.
Key cost factors include:
- Initial gap analysis and quality system audit
- Staff training and internal process upgrades
- Documentation preparation and control systems
- Implementation of ISO 13485 requirements
- Third-party audit and registration charges
- Number of employees and facilities involved
- Use of trusted ISO certification services in Lebanon
- Follow-up audits and certification maintenance
PopularCert ensures smooth certification with cost-effective solutions tailored to Lebanon’s medical and healthcare industries.
Why Choose PopularCert For ISO 13485 Certification in Lebanon?
PopularCert stands out as a trusted provider for ISO 13485 certification in Lebanon, helping medical device manufacturers align with international regulatory and quality standards. Our consultants understand Lebanon’s healthcare landscape and deliver customized solutions that simplify compliance without disrupting operations.
- Specialized ISO 13485 consultants in Lebanon
- Smooth certification process tailored to your operations
- In-depth understanding of Lebanon’s medical device sector
- Clear documentation support, and training
- Proven track record in regulatory compliance and quality control
Work with PopularCert to ensure your medical devices meet the highest standards of safety, consistency, and global market readiness.
GET A FREE CONSULTATION NOW
FAQ
What is ISO 13485 certification?
ISO 13485 certification is an international standard for Quality Management Systems (QMS) in the medical device industry. It ensures organizations meet regulatory requirements, produce safe, high-quality medical devices, and enhance operational efficiency and customer satisfaction.
Why is ISO 13485 Certification important in Lebanon?
ISO 13485 certification in Lebanon is important for ensuring compliance with international regulatory standards, improving product quality, and enhancing operational efficiency. It builds trust with customers, supports market access, and demonstrates a commitment to safety and excellence in the medical device industry.
What are the benefits of ISO 13485 Certification in Lebanon?
ISO 13485 certification in Lebanon offers benefits like improved product quality, regulatory compliance, enhanced customer trust, and access to global markets. It also reduces risks, boosts operational efficiency, provides a competitive edge, and fosters continuous improvement in medical device manufacturing.
How to get ISO 13485 Certification in Lebanon?
To get ISO 13485 certification in Lebanon, work with PopularCert for expert guidance through gap analysis, process implementation, internal audits and final certification audit, ensuring compliance and operational efficiency.