GMP certification in UAE
Get Free Consultation
From PopularCert, businesses in the UAE can get expert help in obtaining GMP certifications through gap analysis, technical documentation assistance, audit and process evaluation coordination. With their help, businesses can better achieve GMP certification and at the same time bolster their reputation regarding safety and quality. The entire certification process includes assessment of compliance, documentation, facility inspection, and process evaluation.
Why GMP Certification is important for you and your business in UAE.
In the UAE, GMP certification is critical for businesses since it merges international standards with product safety and quality. It enables businesses to control specific risks, assuring guideline compliance, and improving process governance and reliability. Further, it enhances the reputation of brands and provides access to new markets both locally and globally. With the commitment to high-quality, safety, and compliant manufacturing asserted through certification, adoption of GMP tilt trades in favor of trust and reliability in global business strengthening competitive edge.
Risks associated with testing a product, including its final stages, cannot be overlooked. All aspects of product manufacturing are accounted for under GMP—these include raw materials and even employee training. Other areas are construction conditions and sanitation, maintenance of equipment and raw materials, production supervision, maintenance, stringent control over documents, and reporting.
How to Get GMP Certification in UAE?
Process to Get GMP Certification In UAE
Consultation and Gap Analysis
PopularCert’s experts begin by understanding your organization’s needs and current practices in manufacturing and quality control. We then conduct a gap analysis to identify areas requiring improvement to achieve GMP certification in the UAE, ensuring your organization is well-prepared to meet international standards for good manufacturing practices.
Planning, Documentation, and Policy Development
Based on the gap analysis, we develop a detailed implementation plan, allocate resources, and assist in creating essential policies and documentation required for GMP certification. These policies and procedures are seamlessly integrated into your existing operations, ensuring compliance with GMP standards and effective implementation in the UAE.
Training and Awareness
We provide comprehensive training for your staff, ensuring they understand the requirements of GMP certification and their role in effectively implementing and maintaining the management system. Our training programs are tailored to meet the specific needs of organizations in the UAE, empowering your team to successfully achieve and sustain GMP certification.
Internal Audit and Management Review
After implementing the GMP management system, we conduct an internal audit to assess its efficiency and identify any non-conformities. Following this, a management review is carried out to ensure the system aligns with your organization's goals and compliance requirements in the UAE, ensuring readiness for GMP certification.
External Certification Audit and Certification
After successfully completing the external audit by the certification body, your organization will be awarded GMP certification. This certification highlights your commitment to high standards of quality management and continuous improvement in manufacturing practices. It demonstrates your dedication to excellence, enhances your credibility, and builds customer trust, especially for organizations in the UAE.
Benefits of GMP Certification in UAE
- Better Product Quality : Having a GMP certificate means your product meets high-quality standards. It helps to cut down flaws and keeps product quality the same.
- Following Regulations : GMP certificate helps businesses to meet legal needs. It decreases risk of legal problems and makes sure products can be sold in many markets legally.
- More Trust from Customers : GMP certificate is a sign of quality that wins customer trust. It makes them sure of the products' safety and effectiveness and that they are made according to industry standards.
- Better Work Efficiency : Using GMP standards often makes work efficiency better. Companies waste less and get better results, improving profit.
- Open to Worldwide Markets : To enter some foreign markets, a GMP certificate is often needed. This certificate lets businesses reach more markets and make more global deals.
- Less Risk : GMP certificate helps companies spot and lessen risks in making their products. It reduces chances of having to recall products, having legal problems, or damaging brand name.
Case Study: Helping a Dubai-Based Skincare Brand Achieve GMP Certification with Confidence
Client Background:
In early 2024, PopularCert was approached by a rapidly growing manufacturer of natural skincare products located in Dubai Silicon Oasis, UAE. The company intended to increase its exports to the EU and GCC regions, but did not have the Good Manufacturing Practices (GMP) certification, which posed as a major compliance hurdle.
The Challenge:
Even though the client possessed modern and well-maintained production facilities, he still encountered numerous obstacles.
Lack of SOPs (Standard Operating Procedures)
Minimum requirements of technical documentation
Insufficient sterilization area protocols
Misunderstanding of UAE GMP for EU comparability (e.g., EC No. 1223/2009)
PopularCert stepped in with a step-by-step strategy:
Gap Analysis:
We conducted an audit for their facility and processes, and documented workflows. An initial audit revealed over 21 non-conformities by reviewing documentation alone.
Documentation & SOP Support:
We developed comprehensive batch records, cleaning logs, and training logs, and also drafted the necessary SOPs which were more than 15 in number, adhering to the GMP standards.
Facility Improvement Recommendations:
To address the criteria for preventing cross-contamination, production areas and storage areas required minor spatial adjustments and better defined area separation.
Training & Internal Audit Prep:
Staff completed GMP awareness training and attended interactive sessions. In addition, we conducted a mock audit so that the team was fully confident and prepared for the final assessment.
Audit Support & Certification:
In just 11 weeks, the client completed the third-party GMP audit, receiving full certification with only one minor observation.
Results:
- GMP Certification achieved in under 3 months
- Product exports approved to Germany and Saudi Arabia
- Enhanced brand trust and partnerships for retail distribution gained.
- Retail orders from healthcare focused clients expanded by 35%.
Client’s Feedback:
“PopularCert helped us streamline the GMP process.” Their understanding of both the UAE and international standards facilitated our compliance in a quick and confident manner. Their assistance proved invaluable.”
Operations Director, Skincare Lab UAEImportance of This:
This example illustrates that GMP certification in the UAE is not a mere compliance exercise it’s a passport for international markets, trust from consumers, and efficiency in operations. PopularCert stands ready to help businesses in cosmetics, food, or pharma with ample local know-how and certification support.
Types Of ISO Certification In UAE
- ISO certification in UAE
- ISO 9001 Certification
- ISO 14001 Certification
- ISO 45001 Certification
- ISO 22000 Certification
- ISO 27001 Certification
- ISO 17025 Certification
- ISO 13485 Certification
- CE Mark Certification
- ISO 20000-1 Certification
- GMP Certification
- HALAL Certification
- SOC-1 Certification
- SOC-2 Certification
Get Free Consultation
Our Clients
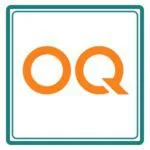
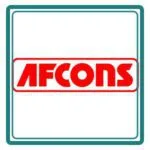
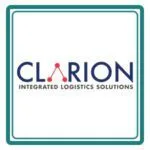
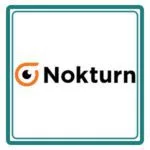
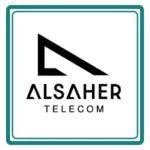
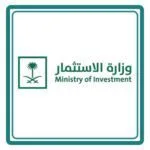
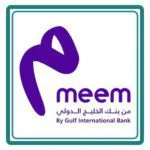
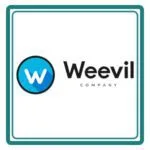
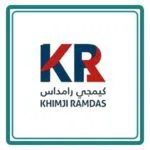
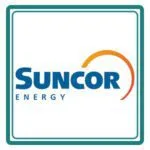
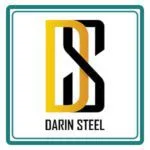
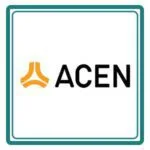
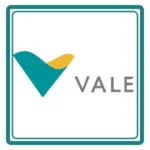
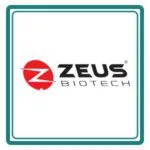
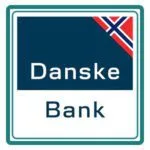

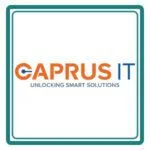
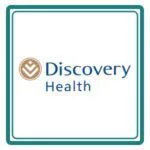
Cost of GMP Certification in United Arab Emirates
The cost of GMP certification in the United Arab Emirates depends on factors such as the size of the organization, the complexity of its manufacturing processes, and its current level of compliance. Typical expenses include gap analysis, training, documentation preparation, audits, and implementation support. PopularCert offers tailored and cost-effective solutions to help businesses in the UAE achieve GMP certification, ensuring compliance with international standards and enhancing operational efficiency in the manufacturing sector.
Why Choose PopularCert For GMP Certification in United Arab Emirates?
PopularCert is an international consulting corporation focused on the services of GMP certification, advisory, and auditing. We are the preferred consultants for GMP certification because of the extensive experience of our loyal, ethical consultants and success track record. As an industry leader in consultancy, certification and auditing services, trust PopularCert for GMP certification in the UAE. Contact us now and get bespoke solutions crafted specifically by our professionals based on the best answers available.
GET A FREE CONSULTATION NOW
FAQ
What is GMP Certification?
Good Manufacturing Practices (GMP) Certification ensures that products are consistently produced and controlled according to quality standards. It applies to industries like pharmaceuticals, food production, cosmetics, and medical devices, focusing on safety, hygiene, and quality.
Why is GMP Certification important in the UAE?
GMP Certification is vital in the UAE as it assures compliance with international standards, enhances product safety, and builds consumer trust. It is crucial for businesses aiming to export products or meet regulatory requirements in competitive markets.
Which industries need GMP Certification in the UAE?
- Pharmaceutical manufacturers
- Food and beverage companies
- Cosmetic and personal care product producers
- Nutraceutical and supplement industries
How to get GMP Certification in the UAE?
Follow these steps to achieve GMP Certification:
- Conduct a gap analysis to evaluate current practices.
- Implement GMP-compliant procedures and policies.
- Train staff on GMP requirements.
- Engage a certification body for an audit and certification process.