GMP certification in Philippines
Get Free Consultation
Ensuring Quality and Safety in Manufacturing in Philippines
Quality assurance in the Philippines focusing on food, pharmaceuticals, and health related products rests on Good Manufacturing Practices (GMP). Regulatory agencies uphold GMP guidelines in the Philippines to guarantee products are produced and managed up to par with quality standards. This protects the health of consumers.
Good Manufacturing Practices, known as GMP, are rules and guides. They help to make sure goods are always made and checked to the same, great quality standards. Shops making food, drinks, medicines, beauty products and medical tools follow these guides a lot.
What is GMP?
The abbreviation GMP stands for Good Manufacturing Practices. These rules address how products are made, tested, and quality checked. They aim to make sure all products are high quality and made in the same way every time. This reduces chances of things like contamination or mislabeling. GMP rules are enforced by groups like the U.S. Food and Drug Administration (FDA) and the European Medicines Agency (EMA). They don’t give specific directions. Instead, they give broad guidelines. By doing this, companies can adjust their processes to meet the guidelines while keeping products safe for consumers.
Why is GMP important?
GMP matters for several reasons:
First, it assures product safety. GMP’s key goal is to guarantee that goods are risk-free for buyers. This is essential in fields like pharmaceuticals and food. Contamination or mistakes can have serious outcomes, even potentially deadly ones. With GMP, there’s a system to prevent these risks. It focuses on the correct management of resources, clean work areas, and precise logs.
Second, GMP stops errors and contamination. During production, even a minor error can significantly affect the final result. GMP is there to avoid these errors, thus ensuring product safety, effectiveness, and quality. It aligns each product with a uniform standard. This comes from a clean workspace, trained staff, and well-maintained tools.
Third, GMP ensures law compliance. Companies selling consumables usually face rules set by domestic or global organizations. GMP rules are often binding by law. So, firms must obey them to avoid issues like product callbacks, fines, or even a total shutdown. In the U.S., for example, the FDA does checks and audits to confirm GMP adherence. Not following GMP can tarnish a company’s image and profits.
How to Get GMP Certification In Philippines ?
Process to Get GMP Certification In Philippines
Consultation and Gap Analysis
PopularCert’s experts start by understanding your organization’s needs and current manufacturing practices. We then conduct a gap analysis to identify areas needing improvement to meet GMP certification standards.
Planning, Documentation, and Policy Development
Based on the gap analysis, we develop a detailed implementation plan, allocate resources, and assist in creating essential manufacturing practices and documentation. These practices and procedures are integrated into your existing framework to ensure GMP certification compliance.
Training and Awareness
We offer thorough training for your staff, ensuring they understand the requirements of GMP (Good Manufacturing Practice) certification and their role in maintaining high-quality standards and processes effectively.
Internal Audit and Management Review
After implementing the GMP system, we conduct an internal audit to assess system effectiveness and identify any non-conformities. Following this, a management review ensures the system aligns with organizational goals and maintains high manufacturing standards.
External Certification Audit and Certification
After successfully completing the external audit by the certification body, your organization will be awarded the GMP certification. This certification highlights your commitment to maintaining high manufacturing standards and continuous improvement. It demonstrates your dedication to product quality, enhancing your credibility, and building customer trust.
Benefits Of GMP Certification In Philippines
- Better Product Quality : Having a GMP certificate means your product meets high-quality standards. It helps to cut down flaws and keeps product quality the same.
- Following Regulations : GMP certificate helps businesses to meet legal needs. It decreases risk of legal problems and makes sure products can be sold in many markets legally.
- More Trust from Customers : GMP certificate is a sign of quality that wins customer trust. It makes them sure of the products' safety and effectiveness and that they are made according to industry standards.
- Better Work Efficiency :Using GMP standards often makes work efficiency better. Companies waste less and get better results, improving profit.
- Open to Worldwide Markets : To enter some foreign markets, a GMP certificate is often needed. This certificate lets businesses reach more markets and make more global deals.
- Less Risk : GMP certificate helps companies spot and lessen risks in making their products. It reduces chances of having to recall products, having legal problems, or damaging brand name.
Types Of ISO Certification In Philippines
Get Free Consultation
Our Clients
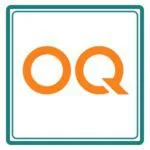
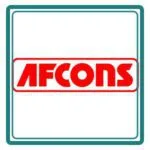
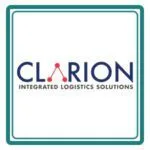
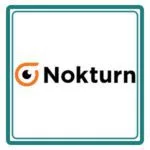
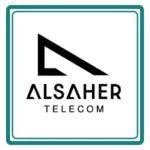
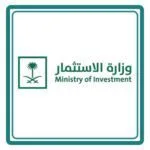
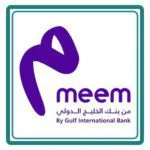
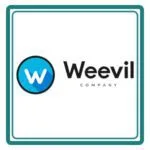
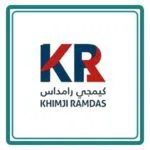
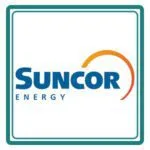
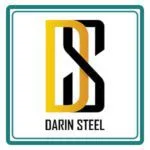
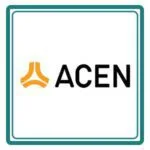
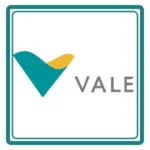
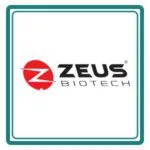
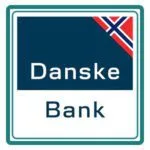

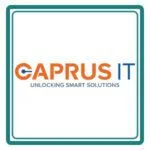
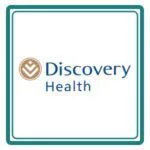
GMP's Contribution to the Development of the Philippine Local Manufacturing Ecosystem
Consistent product safety and hygiene standards are more important than ever as the Philippines’ manufacturing sector expands, particularly in the food processing, pharmaceutical, and cosmetics industries. GMP certification is a game-changer in this situation.
Why this is important
Philippine-based businesses must align their operations with internationally recognized quality benchmarks in light of the growing demand from both domestic and foreign consumers. GMP certification shows that a facility adheres to stringent documentation, risk control, and sanitation guidelines essential in industries like over-the-counter medications, supplements, and food exports.
Instances of increasing significance:
- Food producers in CALABARZON and Metro Manila are looking for GMP in order to comply with ASEAN trade regulations.
- In order to access K-beauty and J-beauty export standards, cosmetic labs in Cebu and Davao are now pursuing GMP.
- GMP serves as the foundation for local pharmaceutical companies throughout Luzon as they get ready for FDA inspections.
Strategic Importance:
GMP certification fosters long-term customer loyalty, market access, and trust in addition to compliance. It serves as the cornerstone for expanding operations and preserving product integrity for Filipino manufacturers in a cutthroat market.
- ASEAN and Access to International Markets
- Improved Adherence to Regulations
- A more robust brand image
- A Competitive Edge in Business-to-Business Transactions
- Better Control of Risk
- Standardization of Procedures Among Facilities
- Access to Additional Certifications
Cost of GMP Certification In Philippines
The cost of GMP Certification in Philippines varies based on factors like the size of your organization, the complexity of your processes, and how prepared your systems are. Good Manufacturing Practices (GMP) ensure your products meet strict standards for quality, safety, and hygiene, which is crucial for industries such as pharmaceuticals, food, and cosmetics. While achieving GMP Certification requires an investment, it delivers lasting benefits, including increased customer trust, regulatory compliance, and access to broader markets. At PopularCert, we simplify the certification journey, ensuring it’s a valuable step for your business.
Ensure product quality and safety with GMP Certification in the Philippines. Contact expert consultants to know how to get and apply for GMP certification at affordable costs.
Why Choose PopularCert For GMP Certification in Philippines?
PopularCert is a globally recognized consulting company specializing in certification, advisory, and auditing services. We are the trusted choice for organizations seeking GMP certification due to our experienced, ethical consultants and proven success record. For GMP Certification in Philippines, choose PopularCert, a leader in consultancy, certification, and auditing services. Contact us now for free consultation, and our experts will promptly provide the best solution tailored to your needs.
GET A FREE CONSULTATION NOW
FAQ
What is GMP Certification?
Why is GMP Certification important for products?
Organizations need this certificate to keep up good production quality, ensure safety, and follow rules.
What are the benefits of GMP Certification?
Getting certified is key for quality and assurance for companies. It boosts trust from clients, opens up new markets, and keeps everything running smoothly. It’s also a way of pledging high-quality output, ensuring what’s produced is safe, and abiding by the rules
What's the timeline for acquiring GMP Certification?
Usually, it’s a matter of months, based on your present regulation adherence.
How do I apply for GMP certification in Philippines?
Choose an accredited certification body, prepare your management system, and submit an application. Consultants can assist with the preparation and certification process.