ISO Certification In Al Jubail
Get Free Consultation
PopularCert is a trusted provider of ISO certification services in Al Jubail, helping businesses implement internationally recognized management systems to improve quality, safety, and environmental performance. ISO certification in Al Jubail includes key standards such as ISO 9001 (Quality Management), ISO 14001 (Environmental Management), ISO 45001 (Occupational Health & Safety), and ISO 27001 (Information Security). Serving industries throughout the Al Jubail Industrial City and surrounding areas, PopularCert offers expert guidance to ensure compliance with global standards, enhance operational efficiency, and strengthen market competitiveness.
What is ISO Certification in Al Jubail?
ISO Certification Al Jubail signifies that a business adheres to internationally accepted standards for quality and management. It demonstrates a company’s commitment to consistent processes, safety, and customer satisfaction. This certification helps Al Jubail businesses enhance credibility, meet regulatory requirements, and strengthen their position in both regional and global markets.
Why ISO Certification is Important for Businesses in Al Jubail?
- Al Jubail is a Developing industrial city where businesses face strong competition and strict regulatory requirements. ISO certification helps companies stand out by ensuring they meet internationally recognized standards for quality, safety, and efficiency. This not only boosts customer trust but also enhances a company’s reputation, making it easier to attract new clients and business partners.
- Beyond gaining market confidence, ISO certification encourages continuous improvement and operational excellence. For Al Jubail’s diverse industries—from petrochemicals to manufacturing—this means streamlined processes, better risk management, and compliance with local and global regulations. Ultimately, ISO certification supports sustainable growth and helps businesses build a strong foundation for long-term success in this dynamic industrial hub.
How to Get ISO Certification In Al Jubail?
Process to Get ISO Certification In Al Jubail
Consultation and Gap Analysis
Organizations in Al Jubail begin by assessing their existing management systems against the relevant ISO standards. This gap analysis helps identify areas for improvement or adjustment.
Planning, Documentation, and Policy Development
Once the gaps are identified, the organization creates the necessary documentation, such as a comprehensive manual, procedures, and records that align with ISO certification requirements.
Training and Awareness
The documented system is then put into practice. Employees are trained on the new procedures and protocols to ensure the system's effectiveness.
Internal Audit and Management Review
Internal audits are conducted to identify non-conformities or areas for improvement, enabling the organization to address them proactively. Top management assesses the system’s overall performance to ensure it aligns with the organization’s strategic goals.
External Certification Audit and Certification
We work closely with accredited certification bodies to facilitate the external audit process for ISO certification. Once the audit is successfully completed, we assist in obtaining the ISO certification. Additionally, PopularCert provides ongoing support, including surveillance audits and expert guidance to ensure continuous compliance and improvements in the management system.
Benefits of ISO Certification in Al Jubail
-
Enhanced Credibility and Reputation : ISO certification boosts the credibility and reputation of organizations in Al Jubail. It signals to clients, partners, and stakeholders that the company adheres to international standards, which fosters trust and confidence.
-
Improved Operational Efficiency : Achieving ISO certification leads to streamlined processes and better resource management. By following structured guidelines and standardized procedures, companies can reduce waste, increase efficiency, and optimize performance.
-
Better Risk Management : ISO standards help organizations identify, assess, and mitigate risks more effectively. This proactive approach reduces the likelihood of problems and ensures better decision-making, particularly in areas related to safety and compliance.
- Increased Market Opportunities : ISO certification opens doors to new business opportunities, both locally and globally. In Al Jubail, where industries are highly competitive, ISO certification can differentiate a business from others and improve its chances of securing contracts.
-
Regulatory Compliance : ISO certification ensures that organizations meet all relevant legal, regulatory, and environmental requirements. It provides a framework for staying compliant with industry regulations, minimizing the risk of fines or legal issues.
-
Continuous Improvement : ISO certification encourages a culture of continuous improvement. By focusing on regular audits, performance reviews, and feedback, organizations can adapt to changes, enhance customer satisfaction, and stay competitive in the marketplace.
Types Of ISO Certification In Al Jubail
- ISO Certification In Al Jubail
- ISO 9001 Certification
- ISO 14001 Certification
- ISO 45001 Certification
Get Free Consultation
Our Clients
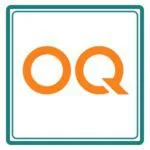
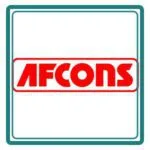
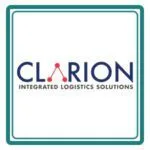
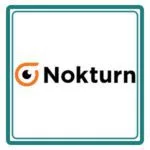
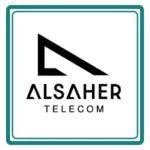
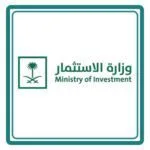
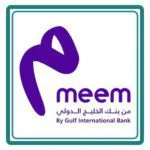
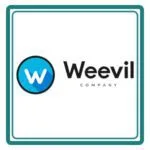
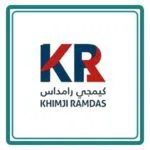
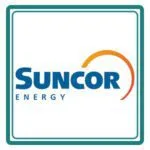
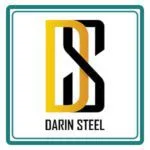
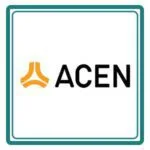
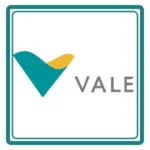
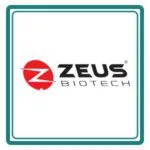
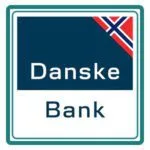

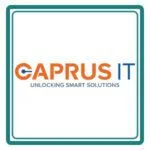
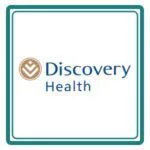
Which Industries in Al Jubail Benefit from ISO Certification?
ISO certification brings valuable improvements to many industries in Al Jubail by boosting quality, efficiency, and trust. Key industries benefiting include:
- Petrochemical and Chemical Manufacturing: Ensures high safety and environmental standards.
- Steel and Metal Production: Improves process consistency and product quality.
- Oil and Gas: Enhances risk management and operational safety.
- Water Treatment Facilities: Supports reliable and safe water management practices.
- Construction and Engineering: Promotes quality control and site safety.
- Logistics and Warehousing: Optimizes supply chain efficiency and compliance.
Adopting ISO standards helps Al Jubail’s industries meet international benchmarks, attract global partners, and drive sustainable growth in a competitive market.
What is the cost of obtaining ISO certification in Al Jubail?
The cost of obtaining ISO certification in Al Jubail depends on your business size, industry, and readiness level. Partnering with the best ISO consultants in Al Jubail ensures a smoother and more cost-effective certification experience.
Key factors affecting ISO certification cost in Al Jubail include:
- Initial gap analysis and system review
- Staff training and awareness sessions
- Documentation development and control
- Internal audits and corrective actions
- Final certification audit by an accredited body
Understanding the ISO certification process in Al Jubail helps organizations budget wisely and avoid unexpected expenses. With professional support, companies can achieve certification efficiently, boosting their credibility and market competitiveness.
Why Choose PopularCert for ISO Certification in Al Jubail?
PopularCert is a trusted leader in ISO certification in Al Jubail, offering expert guidance tailored to your business needs. Our team streamlines the ISO certification process in Al Jubail, ensuring efficient and cost-effective solutions. Recognized among the best ISO consultants in Al Jubail, we help companies achieve compliance and enhance operational excellence.
Key advantages include:
- Personalized support through every certification stage
- Industry-specific ISO implementation strategies
- Affordable and transparent pricing
- Improved credibility and customer trust
- Ongoing assistance for maintaining ISO standards
Achieve international recognition with PopularCert’s expert ISO services in Al Jubail.
GET A FREE CONSULTATION NOW
FAQ
What is ISO certification, and why is it important for businesses in Al Jubail?
ISO certification demonstrates that an organization meets international standards for quality, safety, and efficiency. It helps businesses in Al Jubail build credibility, improve operations, and access new market opportunities.
How long does it take to achieve ISO certification?
The timeline depends on the organization’s size, complexity, and readiness. On average, the process can take 3 weeks to a Month, including preparation, implementation, and audits.
Which industries in Al Jubail benefit most from ISO certification?
Industries like manufacturing, petrochemicals, construction, logistics, and food processing in Al Jubail benefit significantly, as ISO standards enhance quality, safety, and compliance in these sectors.