PDCA Cycle and Risk-Based Thinking in Quality Management Systems
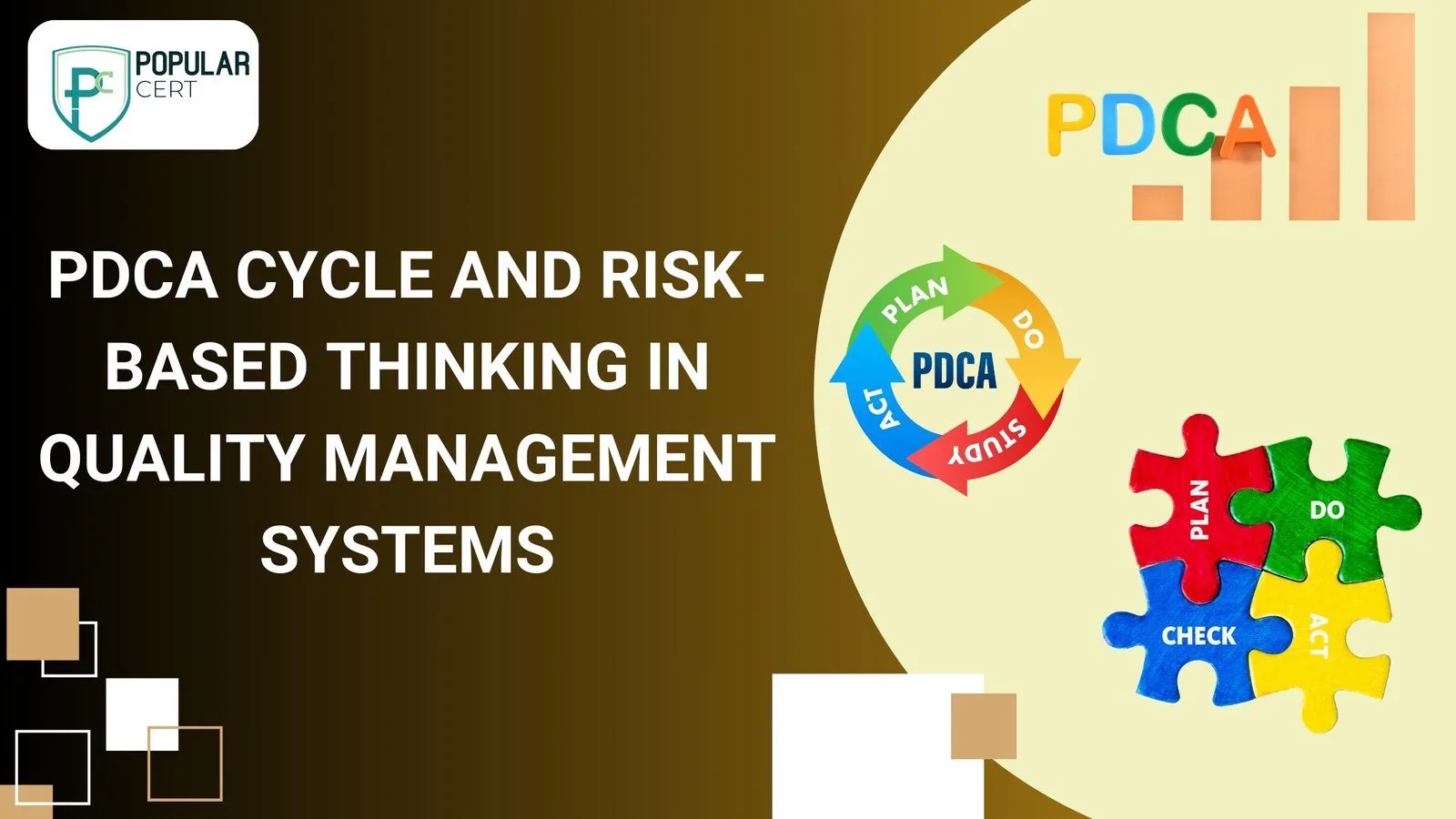
Introduction:
The PDCA (Plan-Do-Check-Act) cycle and risk-based thinking are essential principles in quality management systems like ISO 9001 and AS9100. These approaches help businesses improve efficiency, ensure compliance, and enhance customer satisfaction. By implementing the PDCA cycle, organizations can create a structured process for continuous improvement. Meanwhile, risk-based thinking allows companies to identify potential risks and opportunities, making their operations more resilient. Together, these concepts help businesses stay competitive and meet industry standards.
What is the PDCA cycle?
Plan-Do-Check-Act cycle
The PDCA cycle can be applied to all processes and to the quality management system as a whole, The PDCA cycle can be briefly described as follows:
- Plan establish the objectives of the system and its processes, and the resources needed to deliver results in accordance with customers’ requirements and the organization’s policies, and identify and address risks and opportunities;
- Do implement what was planned;
- Check monitor and (where applicable) measure processes and the resulting products and services against policies, objectives, requirements and planned activities, and report the results,
- Act take actions to improve performance, as necessary.
Risk based thinking
This International Standard requires the organization to understand its context and determine the risks and opportunities that need to be addressed. One of the key purposes of a quality management system is to act as a preventive tool. Consequently, this International Standard does not have a separate clause or sub-clause titled Preventive action.
The concept of preventive action is expressed through a risk-based approach to formulating quality management system requirements
The risk-based approach to drafting this International Standard has facilitated some reduction in prescriptive requirements and their replacement by performance-based requirements.
Although risks and opportunities have to be determined-and-addressed, there is no requirement for formal risk management or a documented risk management process.
What is risk-based thinking?
Risk-based thinking is something we all do automatically.
Example: If I wish to cross a road, I look for traffic before I begin. I will not step in front of a moving car.
Risk-based thinking has always been in ISO 9001 – this revision builds it into the whole management system.
In ISO 9001:2015 risk is considered from the beginning and throughout the standard, making preventive action part of strategic planning as well as operation and review. Risk-based thinking is already part of the process approach.
Example: To cross the road, I may go directly or I may use a nearby footbridge. Which process I choose will be determined by considering the risks.
Risk is commonly understood to be negative. In risk-based thinking opportunities can also be found this is sometimes seen as the positive side of risk.
Example: Crossing the road directly gives me an opportunity to reach the other side quickly, but there is an increased risk of injury from moving cars.
The risk of using a footbridge is that I may be delayed. The opportunity of using a footbridge is that there is less chance of being injured by a car.
Annex SL facilitates integration with other management system standard:
An Integrated Management System (IMS) integrates two or more standards from different disciplines into one. (example: ISO 9001, ISO 14001, OHSAS 18001) Rather than just creating parallel systems, true integration means that similar processes are implemented without duplication or confusion. IMS elements that exist in each system are treated as common resources. They are defined, deployed and managed in the same manner and do not have to deal with multiple, often slightly different interpretations of their roles in executing each standard. Annex SL should make creation of an IMS much easier.
An IMS can streamline a business’s operations by merging different areas of compliance. For example, combining quality, environmental and safety into a single IMS requires fewer resources and is more likely to succeed than maintaining separate management systems for each. Standards can either be combined or integrated.
Conclusion
The PDCA cycle and risk-based thinking are crucial for achieving consistent quality and long-term success. By implementing these approaches, organizations can improve their processes, minimize risks, and create a culture of continuous improvement. An Integrated Management System further enhances efficiency by combining multiple standards into a unified structure. Embracing these strategies helps businesses stay compliant, competitive, and customer-focused.
Types Of Certification
- ISO Certification
- ISO 9001 Certification
- ISO 14001 Certification
- ISO 45001 Certification
- ISO 22000 Certification
- ISO 27001 Certification
- ISO 17025 Certification
- ISO 13485 Certification
- ISO 20000-1 Certification
- ISO 22301 Certification
- ISO 50001 Certification
- ISO 37001 Certification
- IATF 16949 Certification
- ISO 29001 Certification
- ISO 31000 Certification
- ISO 20121 Certification
- ISO 10002 Certification
- ISO 41001 Certification
Get Free Consultation
Our Clients
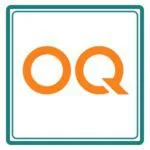
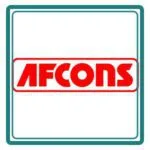
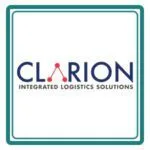
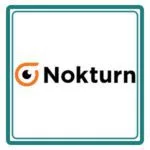
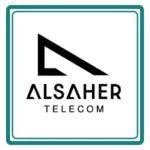
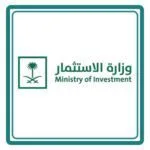
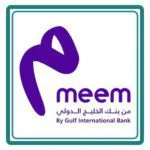
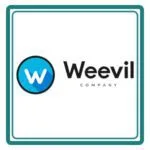
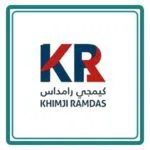
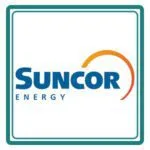
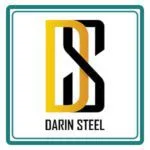
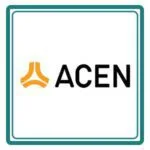
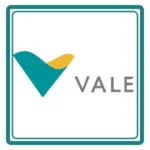
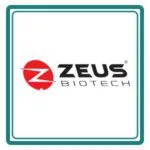
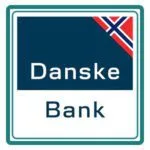

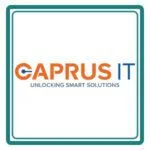
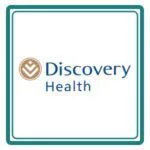
GET A FREE CONSULTATION NOW
FAQ's
What is the PDCA cycle in quality management?
The PDCA cycle is a four-step process (Plan-Do-Check-Act) that helps organizations continuously improve their processes and achieve better results.
Why is risk-based thinking important in ISO standards?
Risk-based thinking helps businesses identify and address potential risks and opportunities, ensuring smooth operations and proactive problem-solving.
How does Annex SL help in integrating management systems?
Annex SL provides a common framework for different ISO standards, making it easier for businesses to integrate quality, environmental, and safety management systems.
Is a formal risk management process required for ISO certification?
No, ISO standards require organizations to determine and address risks but do not mandate a formal risk management process.
How can my company implement an Integrated Management System (IMS)?
An IMS can be implemented by aligning common elements of different standards, reducing duplication, and using a unified approach to compliance and process management.