Risk Management in Quality Systems: A Practical Guide for Businesses
In today’s competitive business environment, having a robust Quality Management System (QMS) is essential for delivering consistent, high-quality products and services. A key part of building an effective QMS is planning and risk management. By identifying potential risks and opportunities, organizations can proactively address challenges and capitalize on favorable conditions. This blog explores how businesses can integrate risk management into their QMS planning, ensuring they meet customer expectations, comply with standards like ISO 9001, and achieve long-term success.
According to Clause 6.1 - Actions to address risks and opportunities
Planning:
All organizations need to develop a QMS that is appropriate for the type of product and services they provide. In planning this, it is important to consider the current context and the needs and expectations of interested parties. This should identify key issues that need to be considered when planning the QMS. The planning at this stage is at a strategic level and consideration of these issues by top management of the organization should result in the development of a quality policy setting out purpose of the organization as well as the strategic direction for the next 3-5 years, the scope of the QMS as well as a determination of the processes needed.
Planning for the delivery of these QMS process can then begin. The purpose of planning is to anticipate potential scenarios and consequences, and as such is preventive in addressing undesired effects before, they occur. Similarly, it looks for favorable conditions or circumstances that can offer a potential advantage or beneficial outcome and includes planning for that worthy of pursuit.
Planning also includes determining how to incorporate the actions deemed necessary or beneficial into the MS, either through objective setting (6.2), operational control (8.1) or other specific clauses of the MS. e.g. resource provisions (7.1), competence (7.2).
The mechanism for evaluating the effectiveness of the action taken is also planned, and can include monitoring. measurement techniques (9.1). internal audit (9.2) or management review (9.3). This is generally what is involved in risk assessment
Risk:
Risk is defined as the effect of uncertainty on an expected result (3.09). The establishment of the QMS is to focus on achieving the expected results.
The risks will vary depending on what the types of products and services offered as well as the nature of the business itself,
For example, a business that sells office stationery may offer a range of “off the shelf products”. The business may have one shop that offers a “walk in service”. Products are purchased from a wholesaler and offered for sale in the shop. Products are low risk themselves but there are perhaps risks regarding supply of product, range of products offered, lack of repeat customers etc. If they are to remain competitive and continue to grow some “market analysis” may be needed to determine what are competitors doing, are there alternative suppliers, should the model change from walk-in to on-line etc. Top management have a role here in reviewing the output of any such analysis and determining the strategic direction for the organization. The QMS then needs to be planned to meet this.
A medical Centre offering a range of medical services to referred patients will have many parties that are more interested, and context issues to consider in the development of their QMS. There are patient safety issues to address as well as having sufficient expertise in house, insurance claims, public vs private funding etc.
Types Of Certification
- ISO Certification
- ISO 9001 Certification
- ISO 14001 Certification
- ISO 45001 Certification
- ISO 22000 Certification
- ISO 27001 Certification
- ISO 17025 Certification
- ISO 13485 Certification
- ISO 20000-1 Certification
- ISO 22301 Certification
- ISO 50001 Certification
- ISO 37001 Certification
- IATF 16949 Certification
- ISO 29001 Certification
- ISO 31000 Certification
- ISO 20121 Certification
- ISO 10002 Certification
- ISO 41001 Certification
Get Free Consultation
Our Clients
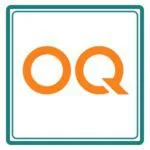
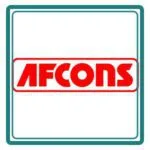
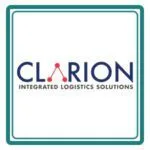
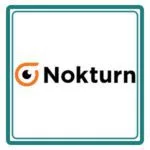
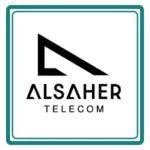
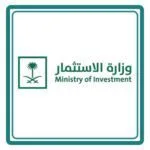
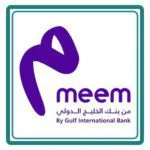
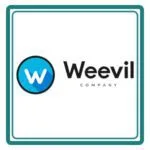
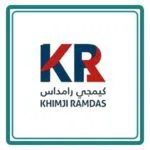
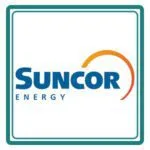
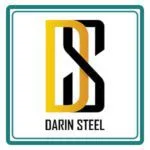
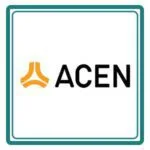
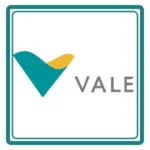
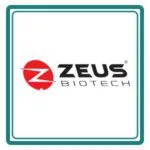
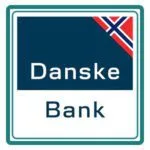

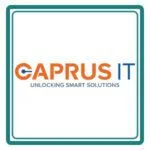
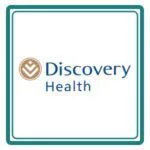
Risk Assessment Method:
There is no requirement in ISO 9001 to use a formal risk assessment method however, there needs to be some consideration of risk qualitatively. The extent and level of risk assessment will depend on the nature and type of business ISO 3100 provides information of risk assessment techniques that can be used but it is down to the organization to determine the best way to evaluate risk and opportunities for themselves, depending on the nature and complexity of the organization’s processes and operations, size, resources available etc.
For example, the organization can use:
- Mental or nuncupative analysis of issues, that can affect to successful completion of any work or project;
- Formalized risk management methods described in ISO 31000, FMEA Manual or other sources,
- Preventive actions procedures, if it is, for example, implemented in effective way in accordance with ISO 9001:2008 requirements,
In determining the risk there needs to be a decision taken on what to do- is action required? Options for dealing with risk can include avoiding the risk, taking the risk to pursue an opportunity, eliminating the risk source, changing the likelihood or consequence, sharing the risk or retaining the risk by informed decision.
Risk-Based ISO Integration
Risk-Framed ISO Integration
Combining ISO 9001’s process control with structured risk frameworks ensures real-time threat identification and prevention.
Structured RM Process
Gap analysis, risk register creation, treatment planning, and documentation provide a clear, traceable risk flow.
Continuous Improvement Loop
Aligns with Plan-Do-Check-Act, embedding risk review and monitoring into every audit and management review cycle.
Data-Driven Decision-Making
Use of metrics like KRIs/KPIs enables proactive prioritization and efficient resource allocation.
Audit-Ready & Compliant
Ensures readiness for internal, supplier, and regulatory audits by maintaining documented risk processes and controls.
Risk Impact:
Where there is a risk that that could impact on conformity of products or service the action taken should be sufficient to address the risk i.e. remove, eliminate or change the likelihood or consequence and indeed priority should be given to risks that impact on conformity of goods and services
During process determination and definition of criteria of its effectiveness the risk that these criteria will not be met and opportunities for improvement of the process effectiveness should be considered.
The risks identified can be prioritized to determine, which of them are acceptable or not. For this can be used mathematical methods, for example FMEA, or acceptability of risks can be determined through consultation with interested parties.
Risk Treatment:
The organization can use following risk treatment methods:
- Risk avoidance: Waiver of processes associated with the occurrence of risk, considered unacceptable. For example, if as a result of customer requirements review, the organization. identified an unacceptable risk, and opted not to tender or fulfil this contract.
- Taking risk: in order to pursue an opportunity. As mentioned above, a risk can be positive. Positive risk can be enhanced by increasing the probability or consequences of it. Positive risk treatment i.e. opportunities for process effectiveness treatment allows us to improve the quality management system as a whole. For example, in the process of internal audit have been identified opportunities for improvement.
Top management can prioritize these opportunities according to the likelihood and magnitude of the positive consequences and take action to introduce/pursue this opportunity to increase the probability and/or positive consequences of these risks.
- Elimination of the risk source: Risk cause determination and elimination. Often to eliminate the risk source the process should be significantly changed. For example, the risk of mix-up of connectors and slots during assembling electronic devices was eliminated by developing a unique configuration of connectors and slots of each type.
- Changing the likelihood: Organization should treat a risk by reducing them for the negative risk and increasing for positive. For example, the risk of nonconforming output of the manufacturing process due to inhomogeneity of the material is a negative risk and its probability can be reduced by purchasing a more homogeneous material.
- Changing the consequences: The consequences can be also treated by reducing the negative and enhance the positive. Can be related to changes in the process itself or related processes. For example, a car tire puncture is a negative risk, and the introduction in the car design of a tires self-swapping system aimed to changing the consequences of such a risk.
- Sharing the risk: Shifting of the responsibility for the risk to other interested parties. For example, a travel agency is responsible for insurance to the travelers in the event of cancellation of flights, etc.
- Retaining the risk: by informed decision. If as a result of risk prioritization negative risk was found not large enough, or there are no cost-effective measures for treating the risk, the organization may decide to retain risks. Risk retention includes informing stakeholders of a risk and monitoring in order to timely detect unacceptable increase of the risk.
For example, there is a negative risk to aviation operations a bad weather in the flight area. It is impossible to eliminate the source of the risk, to change the likelihood and consequences. Consequently, the aeronautical authorities monitor this risk, and if it changes, immediately inform all interested parties.
Risk treatment does not have to be documented. This is firstly an approach, a way of thinking.
Assessment of risk can be subjective, so it is good practice to agree the final decisions on risk with input from at least three individuals from different areas of the organization, e.g. Management team.
Conclusion
Planning and risk management are the backbone of a successful QMS. By anticipating risks, addressing opportunities, and aligning actions with organizational goals, businesses can ensure consistent quality and customer satisfaction. Whether through formal risk assessment methods or strategic decision-making, the goal is to create a system that adapts to challenges and thrives in changing conditions. A well-planned QMS not only safeguards your operations but also drives growth and innovation. Start planning today to build a resilient and future-ready organization.
FAQ
What is the role of risk management in a QMS?
Risk management helps organizations identify potential issues that could affect product or service quality. By addressing these risks early, businesses can prevent problems, improve processes, and seize opportunities for growth.
Is a formal risk assessment method required for ISO 9001?
No, ISO 9001 does not mandate a specific risk assessment method. However, organizations must consider risks qualitatively and decide on the best approach based on their size, complexity, and industry.
How can businesses prioritize risks in their QMS?
Risks can be prioritized based on their impact on product/service conformity and organizational goals. Tools like FMEA (Failure Mode and Effects Analysis) or consultations with stakeholders can help determine which risks are acceptable and which need immediate action.
What are some common risk treatment methods?
Common methods include avoiding the risk, eliminating its source, changing its likelihood or consequences, sharing the risk with others, or retaining the risk with informed decision-making.
How can organizations measure the effectiveness of their risk management actions?
Effectiveness can be measured through monitoring, internal audits, management reviews, and performance indicators. Regularly evaluating outcomes ensures that risks are managed effectively and opportunities are maximized.